Splice Connectors: Characteristics and Applications According to UL/CSA Standards
Hello, folks! Today, we’re diving into quick splice connectors and how to turn wire connections from a headache into pure joy. If you’re still stuck with twists and soldering, this is definitely the place for you. And if you’re already using insulation-displacement connectors (IDCs), I bet you’ll pick up a few tricks you didn’t know about.
This article is all about value—no fluff, just technical specifications, real-world cases, and practical advice. Even if you’ve encountered every type—from classic wire terminals to exotic insulation-piercing connectors—let’s dig deeper into the nuances often overlooked in technical documentation.
Technical Specifications and Contact Details
According to the UL 486A-486B standard, modern splice connectors have the following basic parameters, which may vary by design and manufacturer:
- Operating voltages: 300V to 2000V AC/DC (typical values: 600V for standard and 1000V for industrial versions).
- Wire sizes: AWG 28-4 (0.08-25 mm²), with each model designed for a specific range.
- Maximum current: determined by wire size and installation conditions per NEC Table 310.15(B)(16).
- Contact resistance: 0.2-3 mΩ at 20°C, increasing by 0.4%/°C.
Note: All parameters are specified for copper conductors. Aluminum conductors require special AL/CU-marked versions with separate certification.
"When selecting a splice connector, always choose a model with a current margin of at least 20% above the calculated value to ensure long-lasting and reliable performance."
Fun fact: Contact resistance isn’t constant. Under cyclic loads, it can change exponentially. Typical contact degradation looks like this:
Load Cycles | Resistance (mΩ) | Contact Temperature (°C) |
---|---|---|
0 | 0.2 | 25 |
1,000 | 0.3 | 35 |
10,000 | 0.5 | 45 |
100,000 | 1.2 | 65 |
These data are crucial for designing systems with extended service life.
High-Frequency Operation
When dealing with high-frequency signals, consider the impact of the skin effect on connection characteristics. This phenomenon begins at frequencies as low as 10 kHz, leading to uneven current distribution across the conductor’s cross-section. The skin depth δ (mm) is calculated using the formula:
δ = 66/√f, where f is the frequency in Hz.
Practical consequences:
- At 10 kHz: skin depth ~0.66 mm, resistance increases by 10-15%.
- At 100 kHz: skin depth ~0.21 mm, resistance doubles or triples.
- At 400 kHz: only the conductor’s surface layer is effectively used.
The Tesla Model 3 faced this issue while developing its inverter with PWM frequencies up to 150 kHz. The solution was specialized connectors with silver-plated contacts and complex geometries (increasing surface area) and multi-point contact systems, reducing high-frequency losses by 47%.
To mitigate the skin effect:
- Use stranded conductors like Litz wire with insulated strands thinner than the skin depth.
- Employ contacts with increased effective surface area.
- Use special coatings with high surface conductivity.
These measures are essential in power electronics and PWM-controlled systems.
Extreme Applications
Aviation case: During the development of Boeing 787’s power supply systems, reliable connections were required in temperatures ranging from -65°C to +150°C at reduced pressure. Standard connectors were unsuitable due to the risk of cold flow in plastics. The solution involved composite housings with ceramic inserts and a special thermo-compensating contact mechanism.
"Under extreme temperatures, always check the contact’s torque after the first thermal cycle to catch potential issues early."
Tips for Challenging Cases
Working with fine stranded wires often causes strand fraying. Pro tip: before stripping, wrap the insulation with thin copper wire 1 mm away from the cut. This prevents fraying and ensures a clean strip.
For confined spaces, use angled splice connectors with 45° or 90° turns. According to UL research, these solutions save up to 60% space compared to linear models while maintaining all electrical characteristics.
Professional tricks:
- For high humidity: use dielectric gel (e.g., Dow Corning DC4) with dielectric strength >15 kV/mm. Apply a thin 0.2-0.3 mm layer to the stripped wire.
- For vibration-prone connections: use copper-particle locking paste (1-5 µm) per MIL-DTL-83488D. Increase tightening torque by 10%.
- For shielded cables: fold the shield back onto the jacket at a 175-178° angle and secure with adhesive-lined heat shrink tubing with a minimum 3:1 shrink ratio.
These methods meet IPC/WHMA-A-620E-2022 standards and have been field-tested.
"For frequent reconnections, use nylon cable sleeves before the connector to prevent strand breakage at the housing exit."
Diagnostic hack: To quickly check connection integrity in a wire bundle, use an infrared thermometer at 50% load. Problematic contacts will be 5-7°C hotter than neighboring ones.
Failure Investigation
One of the most instructive cases occurred at a Tier III data center in Dallas. During peak loads, cooling system failures were intermittent. Investigations revealed that standard splice connectors were used in control circuits operating with 20 kHz PWM signals. High-frequency pulsations caused local heating and sporadic temperature sensor failures.
The solution wasn’t obvious: replacing connectors with high-frequency versions only partially solved the issue. Stability was achieved by adding ferrite cores to the connectors, reducing high-frequency noise by 40 dB.
"Always check the signal’s spectral composition before choosing a connector type. What works for DC may fail in pulse modes."
Express Quality Control Methods
Professionals use several quick ways to assess connection quality:
- Thermography: after 10 minutes at nominal load, overheating relative to the wire should not exceed 10°C.
- Micro-vibration test: resistance should not change by more than 10% when tapping the connector.
- Ultrasonic testing: identifies micro-cracks and voids in the contact zone.
These methods provide a rapid, non-destructive connection quality check.
Working with Challenging Materials
Special attention is needed when connecting challenging conductors. Aerospace often uses silver-plated wires, requiring a careful approach. Avoid damaging the silver coating during stripping.
Field Installation Features
Experience installing equipment on offshore platforms highlighted the critical importance of selecting connectors for salt mist conditions. Standard copper-contact splice connectors degraded within 3-6 months. Rhodium-plated connectors proved to be a long-lasting solution, maintaining performance for over five years in marine environments.
Materials and Reliability
Material | Advantages | Limitations |
---|---|---|
Tinned Copper | Low cost, good conductivity | Degrades at T > 100°C |
Silver | Excellent conductivity, oxidation resistance | High cost, sensitive to H2S |
Rhodium | Maximum corrosion resistance | Very high cost |
Material selection directly impacts connection lifespan and reliability under specific operating conditions.
FAQ
How can connection quality be tested?
Measure voltage drop under nominal current, use thermal imaging. The maximum allowable voltage drop per UL is 50 mV under nominal current.
Can aluminum conductors be used?
Only with special AL/CU-marked models per UL 486C.
What happens if the nominal current is exceeded in a splice connector?
Unlike fuses, splice connectors don’t have circuit-breaking protection. Prolonged overcurrent accelerates contact surface degradation due to metal electromigration, increasing resistance and leading to more heat. This avalanche effect can thermally destroy insulation within hours.
Can splice connectors be used in PWM-regulated circuits?
Standard models are not recommended above 400 Hz due to the skin effect and increased eddy current losses. Use specialized versions with silver-plated contacts and ferrite cores certified for frequencies up to 100 kHz with a 30% nominal current reduction.
Conclusion
Splice connector technologies continue to evolve, offering ever-improving solutions for various tasks. The key to successful application remains proper connector selection and adherence to installation techniques. Remember: skimping on connector quality often leads to significant costs for failure remediation.
If you have interesting cases or questions about using splice connectors in unconventional conditions, share them in the comments. Let’s build a knowledge base on this critical topic together!
Смотрите также:
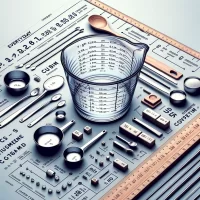
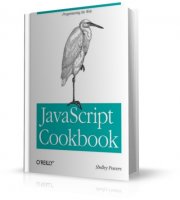
![Kelly L. Murdock - 3ds Max 2011 Bible: tutorials (+DVD) [2010, PDF, ENG]](/uploads/posts/2010-10/thumbs/1287399257_phfugcloyzpeb0t.jpeg)